Ready Mix Concrete – Price, Suppliers, and More
Ready mix concrete, also known as RMC, is manufactured in a factory based on prerequisite mix proportions and designs. This mix is then directly transported to the work site using transit mixers mounted on trucks. Due to the transportation involved, the ready-mix concrete price is higher than the site-mix concrete.
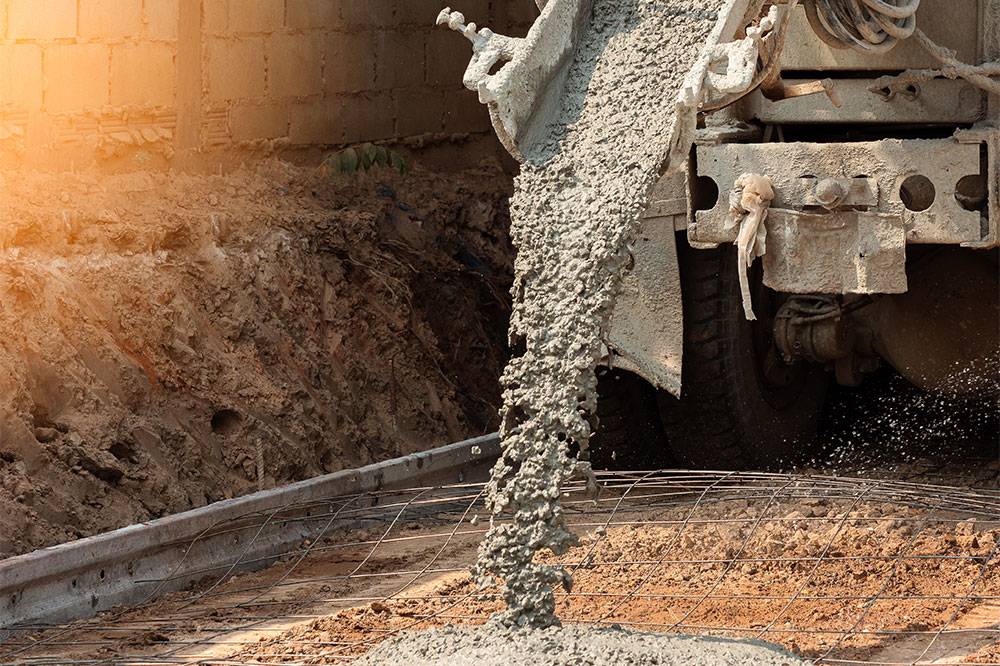
However, this high price is offset by the significant progressive changes in the construction industry brought on by concrete development from being mixed.
Here are a few benefits of ready-mix concrete and the different types.
Benefits of ready-mix concrete
It is high quality
Since ready-mix concrete has sophisticated equipment at the manufacturing plant, it is of higher quality than regular concrete. In addition, the higher quality is also the result of following strict and consistent methods implemented during the manufacturing process. Also, there is a higher degree of controlled testing of the materials used. Also, there is strict control over the process parameters and continuous scrutiny of central key practices to follow during production. These factors ensure that ready-mix concrete is always consistent and of better quality than site-mix concrete.
The production speed is high
All ready-mix concrete suppliers have in place mechanized operations at the manufacturing plant. As a result, ready-mix concrete is always produced at a high and consistent speed. Generally, the production output of concrete from an on-site mixer is about 4 to 5 metric cubes per hour. On the other hand, ready-mix concrete is produced at a staggering high output rate of approximately 30-60 metric cubes per hour in the plant.
Less amount of cement used during production
The production process of ready-mix concrete mandates that standard handling and mixing processes are followed. This ensures all the elements are added in standard proportion. This also applies to cement, which is one of the critical elements for making concrete. In addition, ready-mix concrete requires the use of admixtures and several other cementitious materials. Due to this, the overall consumption of cement is almost lowered by 10 to 12%.
There are fewer chances of human error
The manufacturing process of ready mix concrete is mechanized. It involves the use of precise calculations and processes. Therefore, there is less human intervention involved than site mix concrete. As a result, the probability of human error and dependency on intensive labor is extremely low. Therefore, a more durable structure is obtained. A more durable structure is obtained, thus increasing the service life and saving the life cycle costs.
There is timely delivery
Ready-mix concrete manufacturing processes follow precise measurements and protocols. Moreover, it is made based on mixed designs and quantities determined beforehand. This ensures that whether there is a requirement for small or large quantities of concrete, the ready-mix concrete delivery near the site is done on time.
Common types of ready-mix concrete
There are three major types of ready-mix concrete, these include transit-mixed concrete, shrink-mixed concrete, and central-mixed concrete.
Transit mixed concrete
This is also known as dry-batched concrete because in this type of ready-mix concrete, and all the basic elements are directly poured into the truck mixer. The mixer drum mounted on the truck revolves at high speed during the loading, then its revolving speed is brought down to normal during transit. Furthermore, transit-mixed concrete has three subtypes: concrete mixed at the job site, concrete mixed in transit, and concrete mixed in the yard.
Concrete mixed at the job site
In concrete mixed at the job type, the mixer drum revolves slowly while the concrete is transported to the destination. Once the ruck reaches the site, the drum revolves at high speed just before discharging.
Concrete mixed in transit
The drum revolves at medium speed during transit for concrete mixed in transit type. After about 70 revolutions, the revolving speed slows until the concrete is discharged at the work site.
Concrete mixed in the yard
In this type, the mixing drum containing the concrete revolves at high speed at the yard or manufacturing plant. During transit, the speed is lowered.
Shrink mixed concrete
This type of ready mix concrete uses a combination of mixing at the manufacturing plant and during transit. Initially, the concrete is mixed only partially in the mixer located at the manufacturing site. The mixing is done in a drum mounted on a truck during transit. The extent of mixing required during transit is calculated based on the percentage of mixing done at the central mixing plant. This is generally determined after conducting a series of tests and experiments.
Central-mixed concrete
Manufacturers also label this type of ready-mix concrete as central batching plant concrete. Some ready-mix concrete companies also call this type wet-batch or pre-mix concrete. To make this, the various elements such as cement, admixtures, cementitious materials, and water are mixed thoroughly before loading in the transit truck. During transit to the work site, the mixing drum revolves slowly to keep the concrete mixture from falling apart. Transporting the concrete, the truck mixer acts as an agitator only.
Here are a few benefits of ready-mix concrete and the different types.
Benefits of ready-mix concrete
It is high quality
Since ready-mix concrete has sophisticated equipment at the manufacturing plant, it is of higher quality than regular concrete. In addition, the higher quality is also the result of following strict and consistent methods implemented during the manufacturing process. Also, there is a higher degree of controlled testing of the materials used. Also, there is strict control over the process parameters and continuous scrutiny of central key practices to follow during production. These factors ensure that ready-mix concrete is always consistent and of better quality than site-mix concrete.
The production speed is high
All ready-mix concrete suppliers have in place mechanized operations at the manufacturing plant. As a result, ready-mix concrete is always produced at a high and consistent speed. Generally, the production output of concrete from an on-site mixer is about 4 to 5 metric cubes per hour. On the other hand, ready-mix concrete is produced at a staggering high output rate of approximately 30-60 metric cubes per hour in the plant.
Less amount of cement used during production
The production process of ready-mix concrete mandates that standard handling and mixing processes are followed. This ensures all the elements are added in standard proportion. This also applies to cement, which is one of the critical elements for making concrete. In addition, ready-mix concrete requires the use of admixtures and several other cementitious materials. Due to this, the overall consumption of cement is almost lowered by 10 to 12%.
There are fewer chances of human error
The manufacturing process of ready mix concrete is mechanized. It involves the use of precise calculations and processes. Therefore, there is less human intervention involved than site mix concrete. As a result, the probability of human error and dependency on intensive labor is extremely low. Therefore, a more durable structure is obtained. A more durable structure is obtained, thus increasing the service life and saving the life cycle costs.
There is timely delivery
Ready-mix concrete manufacturing processes follow precise measurements and protocols. Moreover, it is made based on mixed designs and quantities determined beforehand. This ensures that whether there is a requirement for small or large quantities of concrete, the ready-mix concrete delivery near the site is done on time.
Common types of ready-mix concrete
There are three major types of ready-mix concrete, these include transit-mixed concrete, shrink-mixed concrete, and central-mixed concrete.
Transit mixed concrete
This is also known as dry-batched concrete because in this type of ready-mix concrete, and all the basic elements are directly poured into the truck mixer. The mixer drum mounted on the truck revolves at high speed during the loading, then its revolving speed is brought down to normal during transit. Furthermore, transit-mixed concrete has three subtypes: concrete mixed at the job site, concrete mixed in transit, and concrete mixed in the yard.
Concrete mixed at the job site
In concrete mixed at the job type, the mixer drum revolves slowly while the concrete is transported to the destination. Once the ruck reaches the site, the drum revolves at high speed just before discharging.
Concrete mixed in transit
The drum revolves at medium speed during transit for concrete mixed in transit type. After about 70 revolutions, the revolving speed slows until the concrete is discharged at the work site.
Concrete mixed in the yard
In this type, the mixing drum containing the concrete revolves at high speed at the yard or manufacturing plant. During transit, the speed is lowered.
Shrink mixed concrete
This type of ready mix concrete uses a combination of mixing at the manufacturing plant and during transit. Initially, the concrete is mixed only partially in the mixer located at the manufacturing site. The mixing is done in a drum mounted on a truck during transit. The extent of mixing required during transit is calculated based on the percentage of mixing done at the central mixing plant. This is generally determined after conducting a series of tests and experiments.
Central-mixed concrete
Manufacturers also label this type of ready-mix concrete as central batching plant concrete. Some ready-mix concrete companies also call this type wet-batch or pre-mix concrete. To make this, the various elements such as cement, admixtures, cementitious materials, and water are mixed thoroughly before loading in the transit truck. During transit to the work site, the mixing drum revolves slowly to keep the concrete mixture from falling apart. Transporting the concrete, the truck mixer acts as an agitator only.